Inventory receiving and warehousing services
Receiving inventory and warehousing are vital steps in our fulfillment services. Rather than simply storing stock for general warehousing, Autofulfil stores goods that will be fulfilled regularly for customer orders.
Our fulfillment warehousing process involves rigorous inventory management to store inventory ready for quick fulfillment. The result is more cost-effective space for your eCommerce business and a fast, responsive service that keeps customer satisfaction high.
Whether you’re an established eCommerce store or a brick and mortar retailer looking at shipping products further afield, our comprehensive warehousing and fulfillment service is the perfect fit.
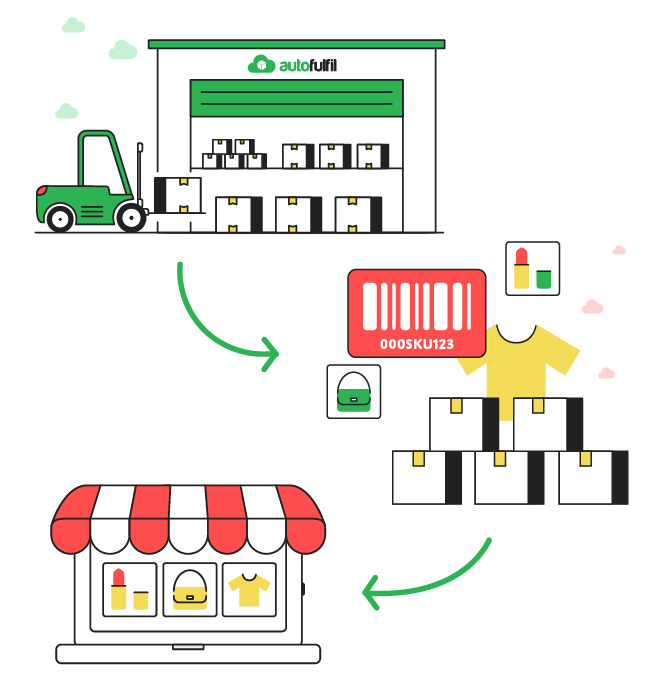
Our warehousing and fulfillment services
The Autofulfil fulfillment centre consists of 100,000 sq ft of warehouse and fulfillment space across three floors in Oranmore, Ireland. Our warehouse includes freight receiving bays, pallet racking, pickable storage bays, pallet pick faces, and assembly and packing stations.
Our secure facility is monitored by a 24/7 security system and security cameras, and we have various security policies in place to keep our clients’ products safe.
Here’s what our fulfillment company can do for you beyond providing warehouse space:
How the process works
Autofulfil goes way beyond leasing warehouse space. From the word ‘go’, we aim to streamline fulfillment for eCommerce companies. That starts by integrating our software with your choice of eCommerce platforms, so orders come straight through to our fulfillment warehouse.
After we integrate our warehouse management system with your eCommerce platform, the next step of our warehousing service is to receive stock for inventory storage in our own warehouse space. As fulfillment providers, this allows us to pick, pack, and ship it the same day your online order is received.
Prior to sending us your inventory for eCommerce fulfillment or B2B order fulfillment, you’ll need to ensure that your products have unique SKU barcodes applied by the manufacturers to ensure fulfillment accuracy, and that the goods in delivery is scheduled in advance with our customer service team for same-day inventory stocking.
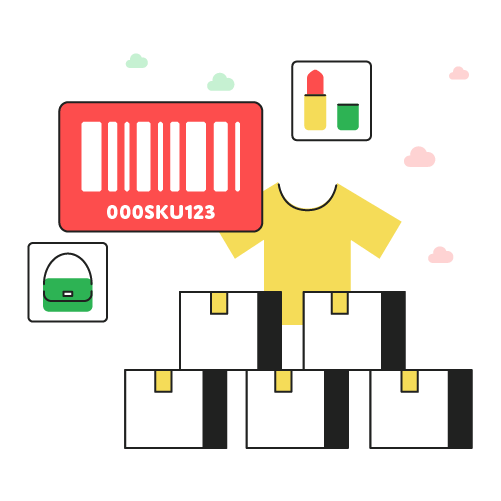
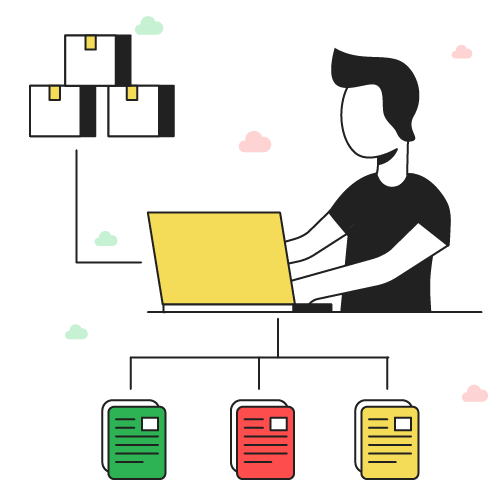
Before storing inventory, we compare what we receive to the delivery docket you send us, and we’ll report back on any stock discrepancies or damaged goods. Once we’ve checked everything into our system, it will become available as in-stock inventory and viewable in our client portal the same day.
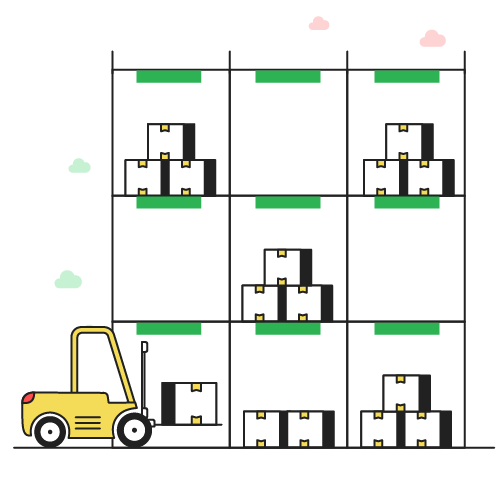
During the inventory receiving process, we’ll assign your products a location in our order fulfillment warehouse for storage, which will either be on a pickable bay or pallet, depending on the number of SKUs stocked and the size of your products. Our bays can hold on average about one pallet of stock.
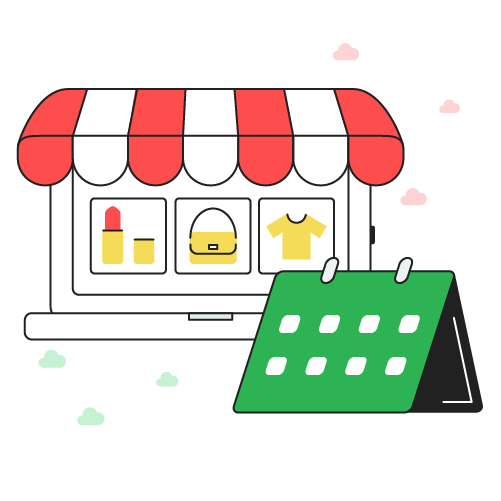
Throughout the fulfillment process, inventory is kept up to date in our system and client portal as goods are received and orders are fulfilled.
Go beyond warehousing with a fulfillment company
Lots of small businesses look for a warehousing company. Outsourcing warehousing alone can reduce storage fees and strengthen your supply chain. But when orders pick up, warehousing and fulfillment companies can assist with even more logistics processes.
Having a third-party logistics company take care of fulfillment needs too can deliver more time and cost savings. Unlike warehousing companies, outsourced fulfillment services can improve accuracy and speed to give customers a better experience when buying from your brand.
Partnering with a fulfillment centre means you win back even more of your time to focus on what you do best. That could be new product development or more active sales and marketing campaigns.
What sets us apart from other fulfillment companies

Only the best fulfillment services
We have a 99.9% order accuracy rate with a same-day fulfillment rate of 99.9% too. In short, our fulfillment operation provides near-flawless eCommerce fulfillment services that many other fulfillment warehouses can’t compete with.

Clear fulfillment fees
With Autofulfil, it’s easy to stay on top of fulfillment costs. You’ll get a fixed fulfillment fee for things like receiving, storage space, and order picking and packing. There’s no hidden costs, so you can budget for fulfillment and price your products accordingly.

Fast and affordable shipping
We ship orders with well-known shipping carriers for a fast service every time. As a global fulfillment provider, we can also assist with international shipments. Thanks to our established relationships and collective buying power, we can secure you better deals for shipping compared to going it alone

Dedicated fulfillment partner
Autofulfil is more than an order fulfillment company. We can cover all bases of your fulfillment network to manage inventory, pick and assemble orders, pack to your requirements, ship to customers, and even deal with returns.

Scalable fulfillment centre
With 100,000 sq ft space, our Irish fulfillment centre gives you all the room you need to grow. Wave goodbye to worries when order volumes increase. Simply scale up your services whenever needs or scale down during quiet periods so you’re never paying too much.

Full visibility
With Autofulfil, you’re always in the know. Access real-time data and analytics through our intuitive client portal with dashboards and reports for inventory levels, fulfilled orders, tracking details, returns processed, and much more.
Request a quote for fulfillment warehousing services
Request a quote for fulfillment solutions today and a fulfillment expert will contact you to answer your questions and provide you with a custom quote tailored to your fulfillment strategy.
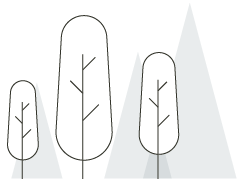